PFAS Treatment Systems (Activated Carbon, Ion Exchange and Membranes)
In a PFAS water treatment system, pressure transducers, differential pressure switches, level switches and indicating gauges, and temperature monitoring are critical for maintaining system efficiency and protecting equipment.
- Pressure transducers monitor and regulate the pressure in filtration units, ensuring the removal of PFAS contaminants without over-pressurizing the system.
- Mechanical pressure switches are used to monitor pump suction/discharge pressures to help ensure efficient operation.
- Differential pressure switches, level switches and indicating gauges track the levels in storage tanks and reactors, activating processes to avoid overflow or emptying.
- Temperature monitoring ensures that the system operates within safe thermal limits, preventing any negative impact on adsorption media or system components.
|
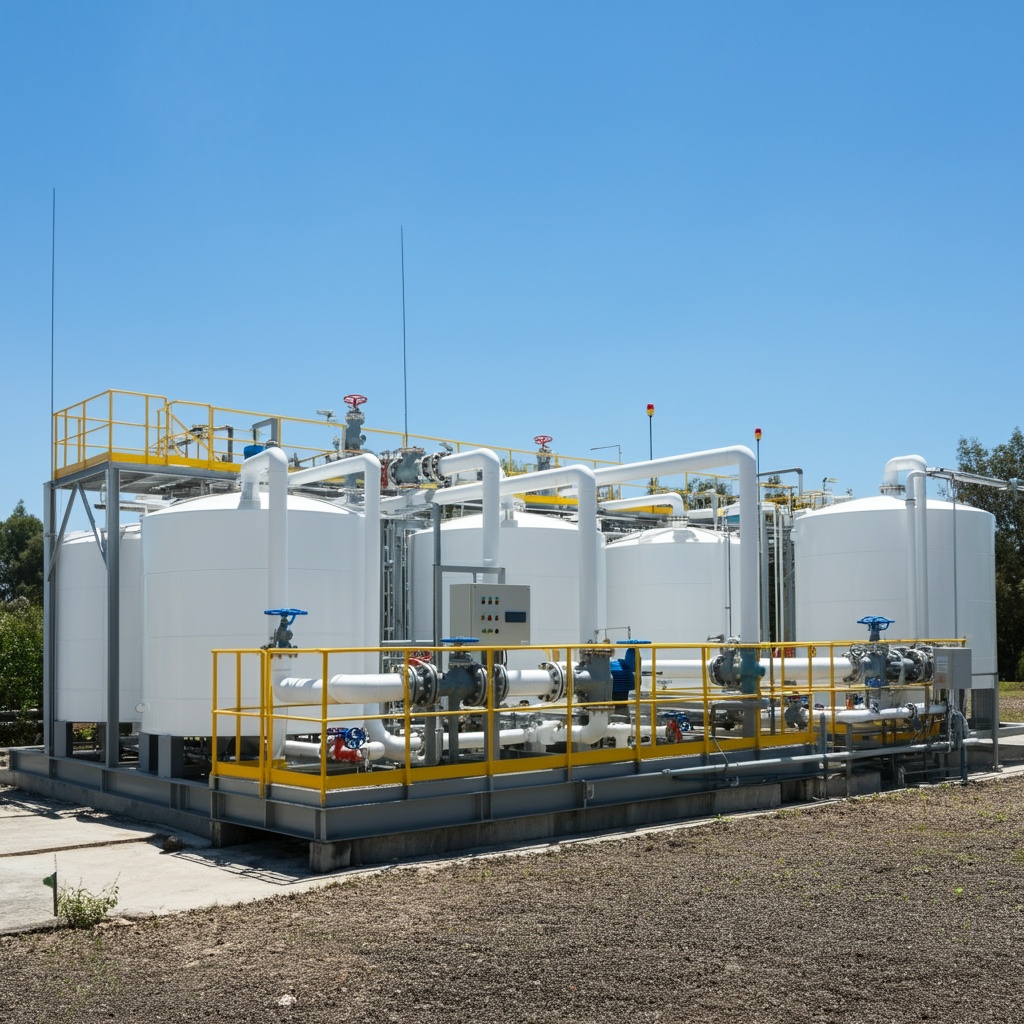
|
Desalination Systems (SWRO, Vapor Compression Brine Concentrator,
Single/Multiple-Effect Evaporator)
In a desalination system, pressure transducers, level switches and indicating gauges, and temperature monitoring play vital roles in ensuring efficient operation and safety.
- Pressure transducers measure and regulate the pressure in pumps and membranes to prevent over-pressurization and ensure optimal water flow.
- Level switches monitor water levels in tanks and reservoirs, triggering actions to avoid overflow or depletion.
- Mechanical Pressure Switches monitor and control pumps that regulate the movement of water through various stages of filtration and maintain efficiency
- Temperature monitoring ensures that the system operates within safe thermal limits, protecting sensitive components like membranes from damage caused by excessive heat.
|
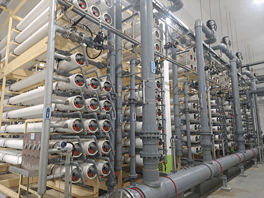
|
Reverse Osmosis Systems
In a reverse osmosis (RO) system, pressure transducers, pressure switches, level switches and indicating gauges, and temperature monitoring are essential for ensuring optimal performance and protection of system components.
- Pressure transducers regulate the pressure across the membranes, which is crucial for efficient water filtration and to avoid damage from over-pressurization.
- Level switches and indicating gauges monitor water levels in feed and permeate tanks, initiating processes to prevent overflow or running dry.
- Mechanical Pressure Switches are used to monitor and control pressure levels in the reverse osmosis system, triggering automatic shutdown or activation of pumps when pressure falls below or exceeds set limits, protecting the membranes from damage due to over-pressurization or insufficient pressure.
- Temperature monitoring ensures the system operates within safe limits, as water temperature directly affects membrane efficiency and lifespan.
|
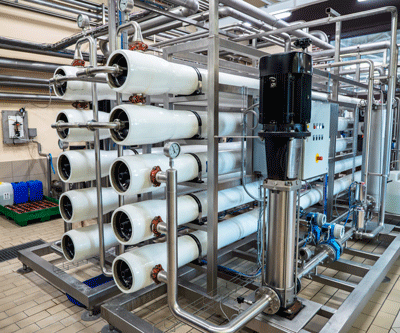
|
Distillation Systems (Multistage Flash Evaporation)
In distillation systems such as multistage flash evaporation (MSF), pressure transducers, level switches and indicating gauges, and temperature monitoring play key roles in ensuring efficient operation and safety.
- Pressure transducers and transmitters monitor the pressure within each stage of the evaporator, which is crucial for maintaining the controlled boiling and condensation processes.
- Level switches and indicating gauges monitor the water levels in the flash chambers and condensate tanks, preventing overflow or dry operation, which could damage the equipment.
- Mechanical Pressure Switches automatically activate or shut down pumps when pressure deviates from set thresholds, safeguarding against over-pressurization or pressure drops.
- Temperature monitoring is vital for controlling the heat input and ensuring the system operates at the optimal thermal conditions, as precise temperature control is essential for maximizing the efficiency of the distillation process.
|
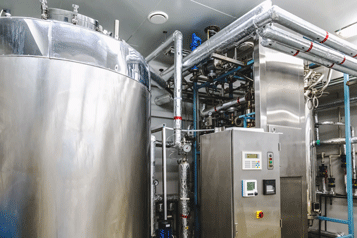
|
Filtration Systems (Ultra-, Micro- and Nano-)
In filtration systems, pressure transducers, level switches and indicating gauges, and temperature monitoring are essential for maintaining optimal performance and protecting equipment.
- Pressure transducers measure and regulate the pressure across filters, ensuring efficient filtration while preventing damage due to excessive pressure.
- Mechanical pressure switches monitor pressure levels and automatically trigger system responses, such as shutting off pumps or opening valves, when pressure exceeds or falls below set thresholds.
- Level switches and indicating gauges monitor the water or fluid levels in tanks and reservoirs, preventing overflow or dry running, which could disrupt the filtration process or damage pumps.
- Temperature monitoring ensures the system operates within safe thermal limits, as excessive heat can affect filtration efficiency and damage sensitive components.
|
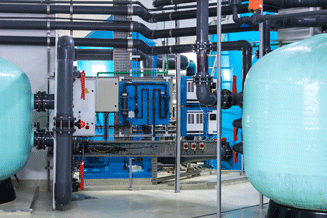
|
Blower & Compressor Packaged Systems
In blower and compressor packaged systems, pressure transducers, level switches, and temperature switches are essential for maintaining efficiency, improving reliability, minimizing downtime, reducing maintenance costs, and safeguarding equipment.
- Pressure transducers and switches monitor and control system pressure, ensuring that compression occurs at optimal levels and preventing over-pressurization, which could damage components.
- Level switches track lubricant or condensate levels, automatically triggering actions to maintain proper lubrication and prevent overflow or system dryness.
- Temperature switches monitor operating temperatures to ensure that the system does not overheat, preventing potential damage or inefficiencies.
|
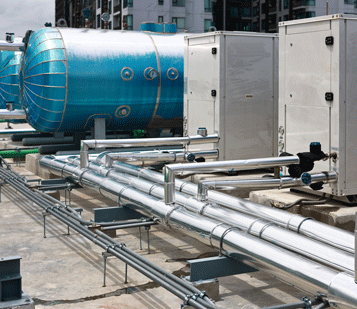
|
Mobile & Containerized Packaged Systems
In mobile and containerized packaged systems, pressure transducers, level switches and indicating gauges, and temperature switches are crucial for maintaining system performance, safety, minimizing downtime, and reducing maintenance requirements while deployed in remote or temporary locations.
- Pressure transducers monitor and regulate pressure within the system, ensuring that pumps, compressors, or filtration units operate within optimal pressure ranges to prevent system failure.
- Level switches and indicating gauges track the fluid levels in tanks or reservoirs, automatically controlling the system to avoid overflows or dry operation, which could cause damage.
- Pressure switches ensure that the system maintains the correct pressure, triggering shutoffs or alarms if pressure deviates from safe limits.
- Temperature switches monitor the thermal conditions to prevent overheating, safeguarding the system from excessive heat that could harm components.
|
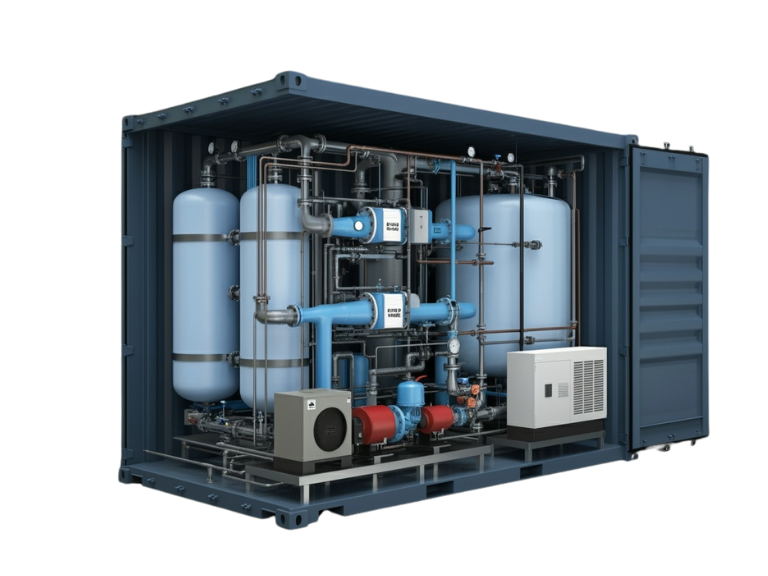
|